Obtenir votre Trinity Audio joueur prêt ...
|
We encounter mirrors daily, yet rarely consider the complex technology behind their creation. How Mirrors Are Manufactured?
Modern mirror manufacturing combines precision engineering, advanced materials science, and meticulous quality control. The process typically involves preparing glass substrates, applying reflective coatings, and adding protective layers before final finishing and framing for various applications like bathroom mirrors, miroirs de vanité, and wall mirrors.
Let’s delve deeper into the fascinating world of mirror manufacturing to understand the intricate processes that transform simple raw materials into the reflective surfaces we rely on every day.
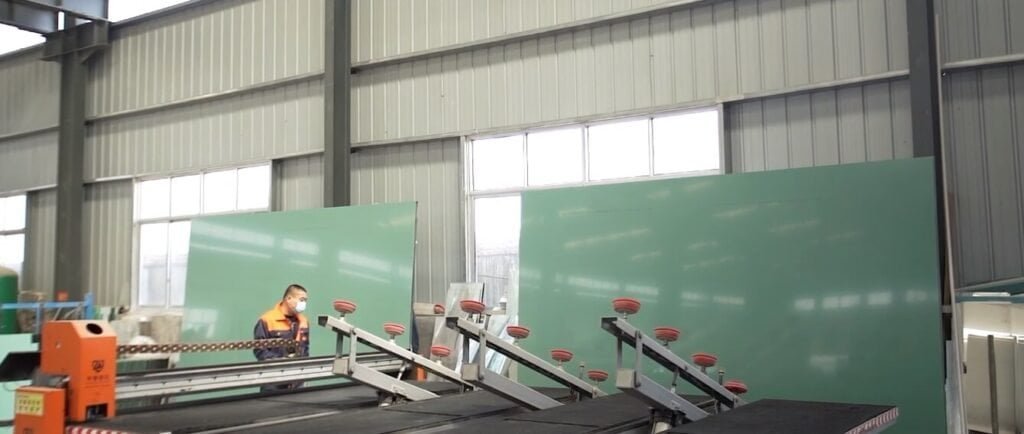
When Were Mirrors Invented?
The idea of reflection has intrigued people since ancient times. The first mirrors date back to 6000 BCE. These early mirrors were made of polished obsidian, a naturally occurring volcanic glass.
The first mirrors were simply polished stones or metals that could produce reflections, though with limited clarity. Ancient Egyptians, Mesopotamians, et Chinese civilizations all developed early forms of mirrors using polished copper, bronze, or other metals, gradually improving techniques over centuries.
The evolution of mirrors throughout history is a testament to human ingenuity in the pursuit of perfect reflection. Early civilizations found that highly polished surfaces of certain metals could reflect images. From there, it was a never-ending quest to improve both the materials and the polishing.
By 1000 CE, glass mirrors backed with metal started to appear, although they remained luxury items available only to the rich. The move from metal to glass-based mirrors was a significant technological leap, providing a much clearer and more durable reflection.
How Did They Make Mirrors in the Old Days?
Ancient civilizations made mirrors by meticulously polishing metal, primarily bronze, copper, or silver alloys. These metals were buffed and polished until they became reflective. It was a laborious process that required a great deal of skill and patience.
Early mirrors were made by polishing metal sheets until they were shiny. Craftsmen used abrasives like sand, ash, and special polishing compounds to create smoother and smoother surfaces that could reflect light and images with some clarity.
Making mirrors in ancient times was a laborious process that required skill. Craftsmen would hammer metal sheets to make them as flat as possible, then use increasingly finer abrasives to polish them. The Romans improved the process by adding tin to copper, creating a bronze alloy that was more reflective.
Some cultures found that by adding precious metals like silver to the surface, the reflection quality was even better. These mirrors were usually small because it was difficult to make large, perfectly flat surfaces with the technology of the day. Nevertheless, they were highly prized possessions. Souvent, they had decorative handles or frames, showing the importance they had in the culture.
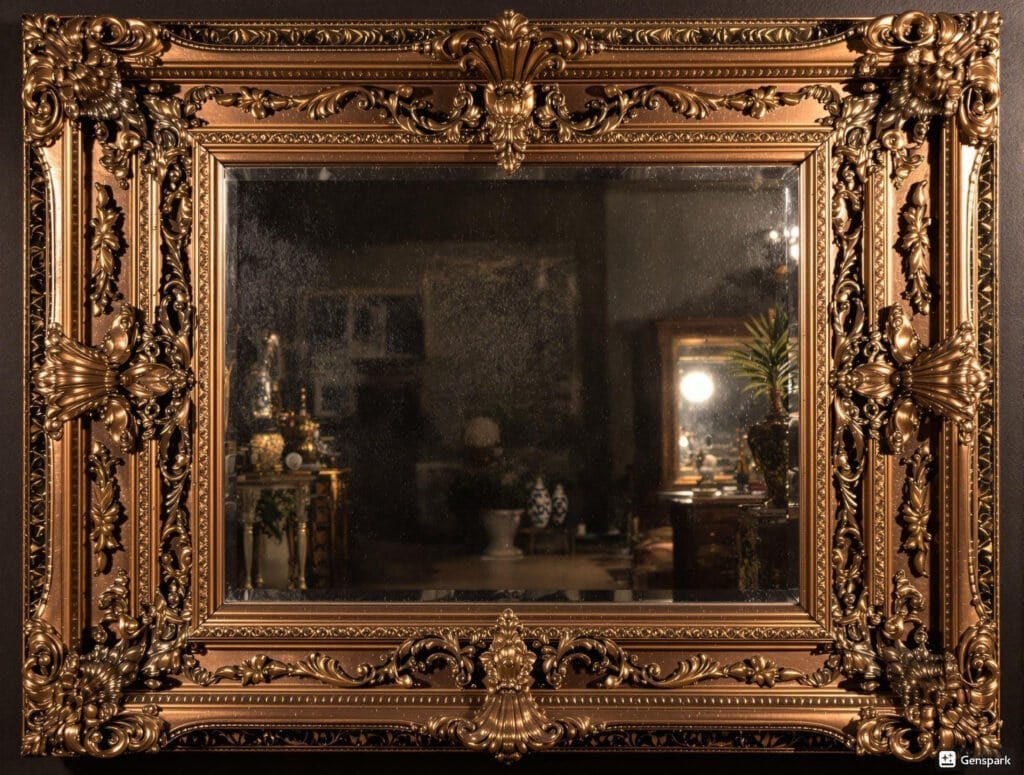
How Were Mirrors Made in the 1700s?
Mirror making took a giant leap forward in the 18th century with the development of the silvering process. By adding a thin layer of silver to the back of a piece of glass, the reflection quality was greatly improved. The silvering process also made the mirror much more durable. Mirrors were no longer just for the very rich.
In the 1700s, mirrors were made by a process called “tin amalgam backing.” Glass plates were covered with a mixture of tin and mercury. This process, perfected in Venice, produced mirrors with much better reflectivity than the old process.
The process was dangerous and complex. Craftsmen would carefully clean glass plates, then apply a thin layer of tin foil onto a perfectly flat surface. Mercury was poured over the tin, creating an amalgam that adhered to the glass when placed upon it. Weights were applied to ensure proper adhesion and squeeze out excess mercury.
The process released toxic mercury vapors, and many of the craftsmen who made these mirrors suffered serious health problems. But the mirrors were of such high quality that they became treasured possessions. The famous Hall of Mirrors at Versailles, completed in 1684, was the ultimate expression of this technology. Le 357 mirrors in the hall demonstrated that France could now compete with Venice, which had previously dominated the glass industry.
What Is a Mirror Made From?
Aujourd'hui, mirrors are made primarily of a glass substrate with a reflective metallic backing and protective layers to prevent damage and oxidation. This basic structure applies to all mirrors, from small mirrors to full-length mirrors.
Standard mirrors are made from float glass coated with a thin layer of silver or aluminum, followed by protective paint layers. The type of glass, reflective material, and protective coatings vary depending on the mirror’s intended use and environment.
The basic ingredient of any mirror is good glass, usually made by the float glass process developed in the 1950s. This process produces perfectly flat glass by floating molten glass on a bed of liquid tin, creating smooth, uniform surfaces perfect for mirrors.
The reflective layer is made of silver, aluminium, or occasionally gold for specialized applications. Silver is the best reflector (over 95%) but tarnishes easily, while aluminum is nearly as good a reflector (à propos 90%) and doesn’t tarnish. After the reflective coating is applied through vacuum deposition or chemical processes, manufacturers add several protective layers, including copper (for silver mirrors) and several coats of paint.
These protective layers prevent moisture and chemicals from reaching the reflective metal, significantly extending the mirror’s lifespan. The composition of these layers varies based on whether the mirror will be used in humid environments like bathroom mirrors or drier settings.
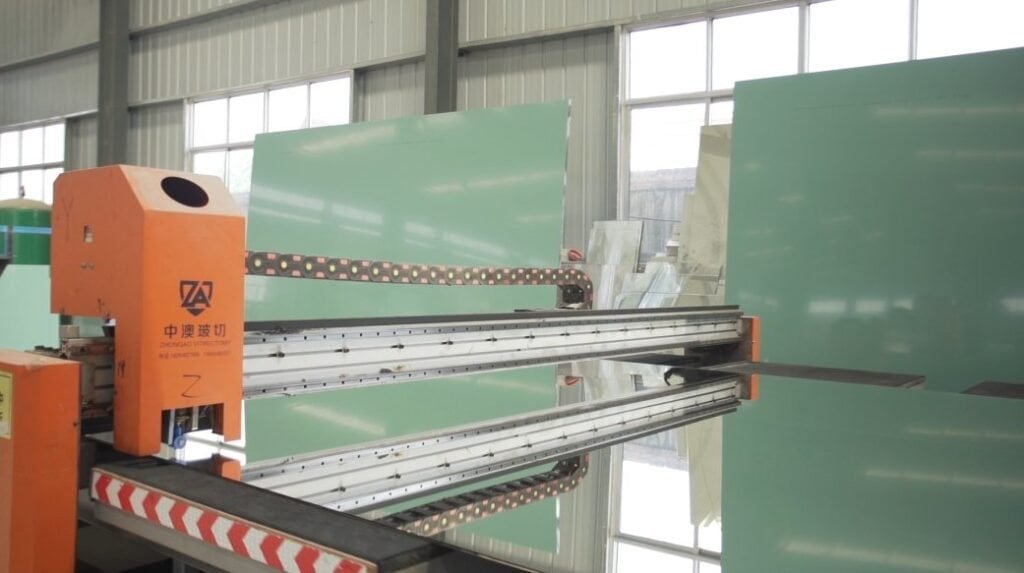
Do They Still Use Silver to Make Mirrors?
Silver is still the preferred metal for high-quality mirrors because it provides a superior reflection. Cependant, aluminum has become popular for many commercial applications, such as wall mirrors.
Aujourd'hui, high-quality mirrors are still made with silver because it reflects about 95-99% of the visible light, creating the clearest images. Cependant, aluminum is used for less expensive mirrors or for special applications because it is more durable and less expensive.
The choice between silver and aluminum for mirror manufacturing involves several considerations. Silver provides unmatched reflective quality, making it ideal for precision instruments, high-end vanity mirrors, and optical applications where image clarity is paramount.
The downside to silver is that it’s more expensive, and you have to take extra steps to protect it from tarnishing and oxidation. Aluminum, d'autre part, est à propos de 90% as reflective as silver. It’s extremely durable, doesn’t corrode, and is less expensive to produce. In recent years, improved application methods have made aluminum mirrors almost as good as silver mirrors.
Most mass-produced mirrors use aluminum. Silver is used for high-end and specialty mirrors. Some manufacturers have developed hybrid methods and new alloys that try to combine the best of both worlds. It’s interesting to see that even with this centuries-old technology, people are still innovating in the mirror-making business.
Are Mirrors Hard to Make?
Making really good mirrors requires precision, special equipment, and strict quality control. While the process of making a basic mirror has been simplified through industrialization, making a perfect reflective surface is still technically difficult.
You have to control the quality of the glass, the thickness of the coating, the environment, and the cleanliness of the surface. Commercial manufacturing has standardized these processes, but making big, perfect mirrors is still a sophisticated industrial process.
The complexity of making mirrors varies widely depending on the type and quality of mirror you want to produce. Mass-producing standard bathroom mirrors and small mirrors has been streamlined through automation, but you still need a clean room to keep dust from getting on the reflective surface.
When you get into specialized mirrors like those used in telescopes or scientific instruments, the difficulty of manufacturing them goes through the roof. These precision mirrors require glass with virtually no imperfections and reflective coatings applied with atomic-level precision. Making large mirrors is even more difficult because keeping a large surface perfectly flat is a huge challenge.
Temperature changes during the manufacturing process can cause imperceptible warping that affects the quality of the reflection. Modern mirror factories use lasers and computer-controlled application techniques to overcome these challenges. Even though we’ve industrialized the process of making basic mirrors, making a perfect mirror is still as much an art as it is a science.
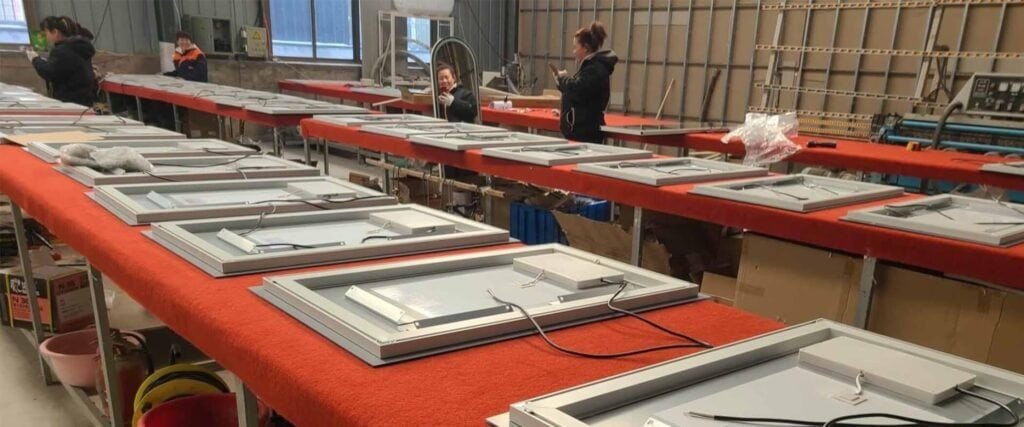
How Are LED Mirrors Made?
LED mirrors are a combination of traditional mirror manufacturing and integrated lighting technology. These innovative bathroom mirrors and vanity mirrors have LEDs built into them in specific locations to provide added functionality and aesthetics.
LED mirrors are made by integrating energy-efficient LED lighting systems into specially designed mirror structures. The process includes creating channels or mounting points for the LED components, installing diffusers for even light distribution, and integrating control systems for adjustable lighting features.
The production of LED mirrors is the perfect marriage of traditional craftsmanship and modern technology. It starts with high-quality mirror glass made using standard processes. The mirror is then custom-cut to accommodate the LED lighting components, which often requires precision edge work and safety treatments.
Engineers design specific light patterns based on the mirror’s intended use. Par exemple, bathroom mirrors might feature practical, Même l'illumination. Vanity mirrors often include more focused lighting optimized for makeup application. The LED components are mounted behind frosted sections of the mirror, around the perimeter, or sometimes within the mirror itself using special two-way mirror technology.
These LEDs are tied to control systems that can include touch sensors, motion detectors, or wireless connectivity for integration with your smart home. Many of the modern LED mirrors have additional features like anti-fogging heating elements, Haut-parleurs Bluetooth, a digital clock, or a magnification panel.
The electrical components have to be sealed and insulated very carefully to be safe in a humid environment like a bathroom. The integration of technology with traditional mirrors has revolutionized the industry. You now have products that provide functional lighting and look great.
How Mirror Is Made from Sand?
The journey from sand to mirror starts with turning silica sand into glass. It’s an amazing process of melting and forming. This transformation takes something that’s just ordinary granular material and turns it into a transparent solid.
Mirror production begins with high-purity silica sand. It’s melted at about 1700°C. Other materials like soda ash and limestone are added. Then it’s cooled into glass sheets through the float glass process before being further processed into mirrors.
The transformation of sand into a mirror is one of the most incredible manufacturing feats of mankind. It starts with selecting high-grade silica sand that has few impurities. This sand is mixed with sodium carbonate (soda ash), calcium oxide (limestone), and other additives that help lower the melting point and improve the properties of the glass.
This mixture is heated in furnaces to approximately 1700°C (3092°F). It becomes a molten liquid. In modern glass production, this molten glass is poured onto a bed of molten tin in a carefully controlled atmosphere, a technique known as the float glass process. As the glass “floats” on the perfectly flat surface of the tin, gravity and surface tension combine to create an exceptionally smooth sheet with uniform thickness.
Once it’s cooled and annealed to release internal stresses, the glass is cut to size. This float glass then becomes the substrate for mirror manufacturing. It’s an amazing example of how a common material like sand can be transformed through heat and precision engineering into a material with completely different properties.
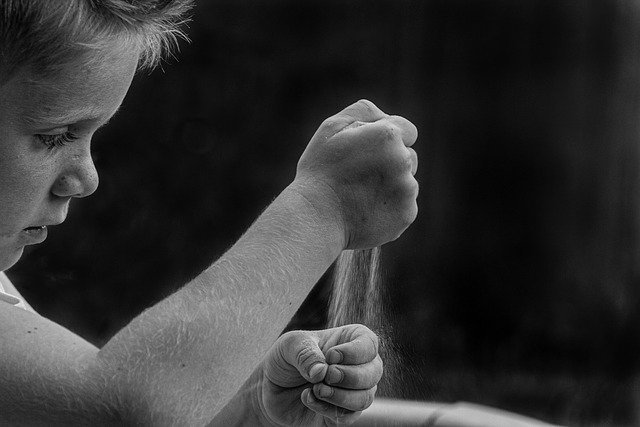
How Is Mirror Made from Glass?
Transforming ordinary glass into a reflective mirror involves a precise sequence of cleaning, applying a metallic coating, and adding a protective layer. Each step must be executed with exacting standards to achieve perfect reflectivity.
To make glass into a mirror, you have to go through a multi-step process: clean it thoroughly to remove all impurities, apply a sensitizing solution, deposit a reflective metal layer (généralement argent ou en aluminium), and then apply protective paint layers to protect the delicate metal coating.
The process of turning glass into a mirror starts with preparing the glass surface. Any imperfections, dust, or oil on the glass will result in defects in the final mirror. Donc, industrial cleaning processes often involve multiple stages of detergent washing, deionized water rinsing, and sometimes ultrasonic cleaning for the highest quality mirrors.
Once the glass is perfectly clean, it is sensitized (usually with a tin chloride solution) to ensure good adhesion of the metal layer. In the case of silver mirrors, the glass is sprayed with a silver nitrate solution that chemically deposits a thin layer of pure silver onto the glass surface. In the case of aluminum mirrors, the metal is applied through vacuum deposition, where aluminum is evaporated in a vacuum chamber and condenses onto the glass. This reflective layer is incredibly thin—only 1,000 nanometers or less.
After the metallic coating, they add protective layers. If it’s a silver mirror, they’ll add a layer of copper. Then they’ll add multiple coats of paint to protect the delicate metal from oxidation, scratches, and chemical damage. The entire process requires precise environmental controls. Variations in temperature and humidity can affect the chemical reactions and the quality of the coating.
What Quality Control Measures Ensure Mirror Durability?
To make sure the mirrors last, they test them for reflectivity, coating adhesion, resistance to environmental factors, and structural integrity. These quality control procedures are essential whether we’re talking about bathroom mirrors or full-length mirrors.
Quality mirrors are tested for reflection, copper accelerated salt spray, humidity resistance, and adhesion. These tests ensure the mirror will perform as expected for the life of the product in various environments.
Mirror manufacturers have quality control systems in place to make sure their mirrors will work for years. They use optical testing to measure reflectance values to make sure mirrors meet specific standards for clarity and light reflection.
For bathroom mirrors and other products designed for humid environments, environmental testing becomes critical. They’ll put samples in humidity chambers to simulate years of being in a bathroom in a matter of weeks. Salt spray testing helps them predict how being near the coast might affect the mirror over time.
Physical durability testing includes abrasion resistance to make sure the reflective coating won’t scratch easily, impact testing for safety mirrors, and adhesion testing to make sure all the layers stay bonded under stress. They also do chemical resistance testing using common household cleaners to make sure the mirrors will stand up to typical cleaning products.
For LED mirrors, they also do electrical safety testing and measure light output. These quality control procedures help manufacturers find weaknesses in their products before they get to you, so they can continue to improve their manufacturing processes. The best mirror manufacturers exceed industry standards and offer extended warranties as proof of their confidence in the durability of their products.

How Are Custom Mirrors Manufactured?
Creating custom mirrors requires special techniques to handle unique shapes, tailles, and finishes. Whether you’re making small mirrors with decorative edges or oversized wall mirrors, you need to adjust your manufacturing process.
Custom mirrors are created using precision cutting technologies, specialized edge treatments, and custom coating applications. Manufacturers work with designers and customers to take specific requirements and turn them into manufacturing specifications before they start the custom production process.
The custom mirror manufacturing process starts with detailed specifications that spell out the exact dimensions, edge treatments, mounting requirements, and any special features such as beveling or antiquing effects. For mirrors that are uniquely shaped, computer-aided design is used to create precise cutting patterns that guide diamond-tipped tools or high-pressure water jets that cut the glass substrate.
Edge work is a big deal when it comes to custom mirrors. You can have anything from a simple polished edge to a fancy beveled edge that creates a prism effect. If you’re making big mirrors or full-length mirrors, you have to solve some unique structural problems to keep them from warping and to make sure they’re safe to hang. This might involve using thicker glass or doing something to reinforce the glass.
Custom finishes can be an antiqued look created by controlled decay of the reflective layer, tinted mirrors made by using colored glass or special coatings, or artistic things like hand-etching or sandblasting to create designs. Many custom mirrors also have custom frames that not only look good with the mirror, but also provide additional structural support.
The combination of these options gives you an infinite number of design possibilities. It allows architects and designers to create mirrors that fit perfectly in any space, whether it’s a residential bathroom or a commercial interior.
Conclusion
Mirror manufacturing combines ancient knowledge with modern technology to produce the reflective surfaces we rely on daily. From simple bathroom mirrors to sophisticated LED designs, understanding how mirrors are manufactured reveals the remarkable craftsmanship behind these everyday objects.
- Pour apprendre à choisir le bon miroir de salle de bain, cliquez ici.
- Pour apprendre à installer un miroir, choisissez ici.
- Pour apprendre à choisir le miroir de bonne taille, cliquez ici.
- Pour apprendre comment les miroirs sont fabriqués ici.
- Cliquez ici et vous apprendrez pourquoi nous avons l'air mieux dans les miroirs.
- Cliquez ici, vous découvrirez le haut 10 fabricants de miroir LED pour 2024.
- Cliquez ici pour découvrir pourquoi ma lumière miroir de vanité ne s'allume pas?
- Découvrez quelle est la taille du miroir de salle de bain?Cliquez ici
- Cliquez ici si vous ne savez pas comment nettoyer votre miroir
- Pour savoir comment réparer le miroir du capteur tactile ne fonctionne pas, cliquez ici